How to Build a Successful Biodiesel Plant with the Right Manufacturer
- xires57140
- Apr 10, 2023
- 5 min read
Understanding the Biodiesel Manufacturing Process
Biodiesel is a renewable, biodegradable, and environmentally friendly alternative to traditional fossil fuels. It is produced through a chemical reaction between vegetable oil, animal fat, or recycled cooking oil and an alcohol, usually methanol or ethanol. The process of producing biodiesel involves several stages, including pre-treatment, transesterification, washing, and drying.
During pre-treatment, impurities are removed from the feedstock, such as water, free fatty acids, and solid contaminants. Transesterification is the main chemical reaction that converts the feedstock into biodiesel, by reacting it with the alcohol and a catalyst. After transesterification, the mixture is separated into two phases, glycerol and biodiesel, by gravity.
The glycerol is then removed and the biodiesel is washed and dried to remove any remaining impurities. Finally, the biodiesel is ready to be used as a fuel or blended with diesel in various proportions. The biodiesel manufacturing process requires careful control of several parameters, such as temperature, pressure, and reaction time, to ensure optimal yields and quality.
Understanding the biodiesel manufacturing process is crucial to building a successful biodiesel plant with the right manufacturer, as it will enable you to make informed decisions about feedstock selection, plant design, and process optimization.
Selecting the Right Biodiesel Plant Manufacturer
Selecting the right biodiesel plant manufacturer is a critical step in building a successful biodiesel plant. A reputable manufacturer should have a proven track record of delivering high-quality, reliable, and efficient biodiesel plant equipment and services. When selecting a manufacturer, it is essential to consider several factors, such as experience, expertise, reputation, and customer support.
Look for a manufacturer that has a deep understanding of the biodiesel industry and can offer tailored solutions to meet your specific needs. Also, consider the manufacturer's experience in designing and building biodiesel plants of similar size and complexity as yours. A reputable manufacturer should be able to provide you with references and case studies of previous projects. Reputation is also an important factor to consider, as it reflects the manufacturer's ability to deliver on promises and provide high-quality products and services.
Check for reviews, testimonials, and ratings from previous customers. Finally, consider the level of customer support that the manufacturer provides. A good manufacturer should offer comprehensive support throughout the entire process, from plant design to installation, commissioning, and maintenance.
They should be able to provide training, spare parts, and technical assistance to ensure that your biodiesel plant operates at optimal performance. By selecting the right biodiesel plant manufacturer, you can ensure that your investment is well spent, and your plant is designed and built to last.
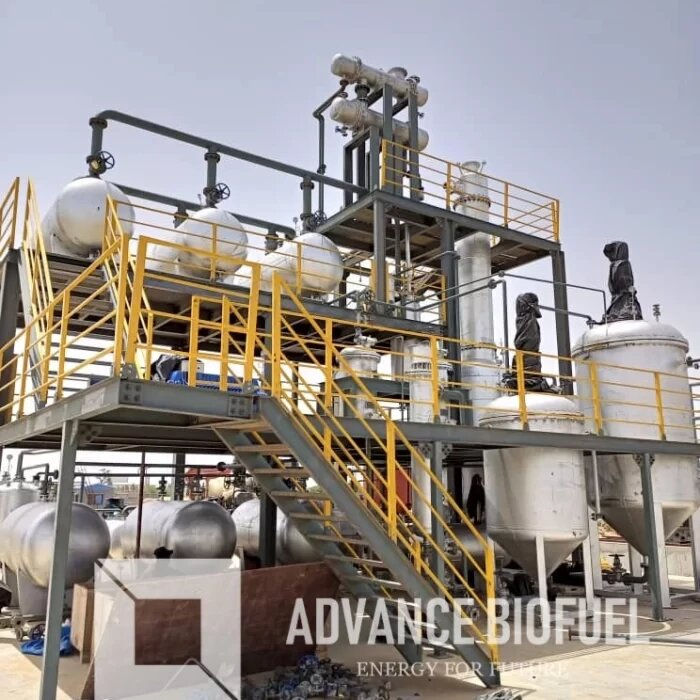
Designing and Building Your Biodiesel Plant
Designing and building a biodiesel plant requires careful planning, engineering, and construction. The first step is to develop a comprehensive project plan that includes a detailed feasibility study, cost analysis, and risk assessment. The feasibility study should evaluate the availability and quality of the feedstock, the local regulatory environment, and the market demand for biodiesel. It should also assess the technical and economic viability of the project. The cost analysis should estimate the total project cost, including equipment, construction, installation, and operational expenses. The risk assessment should identify and evaluate the potential risks and challenges associated with the project, such as environmental, regulatory, and market risks.
Once the project plan is finalized, the next step is to design the biodiesel plant. The design should take into account the feedstock characteristics, production capacity, and process efficiency. It should also consider the local regulatory requirements and safety standards. The design should be developed in close collaboration with the biodiesel plant manufacturer to ensure that the equipment is optimized for the specific plant design.
After the design is completed, the construction and installation phase can begin. This involves site preparation, foundation construction, and equipment installation. It also involves electrical and mechanical engineering, piping and instrumentation, and safety systems installation. During the construction and installation phase, it is crucial to ensure that all work is performed according to the design specifications, safety standards, and local regulations.
Finally, the biodiesel plant can be commissioned and put into operation. This involves testing the equipment, tuning the process, and verifying that the plant meets all regulatory requirements and safety standards. The commissioning phase should be conducted by experienced professionals and should involve training for the plant operators.
Designing and building a biodiesel plant is a complex process that requires a multidisciplinary approach and close collaboration between the plant owner, the biodiesel plant manufacturer, and other stakeholders. By following a rigorous project plan and design process, and working with reputable and experienced partners, you can build a successful and sustainable biodiesel plant.
Ensuring Regulatory Compliance for Your Biodiesel Plant
Ensuring regulatory compliance is a crucial aspect of building and operating a biodiesel plant. Biodiesel production is subject to numerous federal, state, and local regulations, including environmental, health, and safety standards. Compliance with these regulations is not only a legal requirement but also essential for the sustainability and reputation of your biodiesel plant.
The first step in ensuring regulatory compliance is to understand the regulatory landscape and the specific regulations that apply to your biodiesel plant. This may involve consulting with regulatory experts, attending industry conferences, and reviewing regulatory guidelines and standards.
The next step is to incorporate regulatory compliance into your plant design and operation. This may involve implementing environmental and safety management systems, such as ISO 14001 and OHSAS 18001, respectively. It may also involve conducting environmental impact assessments and developing emergency response plans.
Once the plant is operational, ongoing compliance monitoring is essential. This may involve regular reporting to regulatory agencies, maintaining compliance records, and conducting periodic audits and inspections. It is crucial to identify and address any non-compliance issues promptly and proactively to avoid potential legal and reputational risks.
Compliance with regulations also involves ensuring the sustainability and social responsibility of your biodiesel plant. This may involve implementing sustainable sourcing practices for feedstock, such as using waste or low carbon intensity feedstocks, and supporting local communities through job creation and economic development.
In summary, ensuring regulatory compliance is a critical component of building and operating a successful and sustainable biodiesel plant. By understanding and complying with the relevant regulations, incorporating compliance into plant design and operation, and maintaining ongoing compliance monitoring, you can avoid potential legal and reputational risks and contribute to a more sustainable future.
Maximising Efficiency and Profitability of Your Biodiesel Plant
Maximizing the efficiency and profitability of your biodiesel plant is essential for long-term success. Several factors can impact the plant's efficiency and profitability, such as feedstock quality, process optimization, energy consumption, and product quality.
One way to maximize efficiency is to optimize the biodiesel production process. This involves identifying and minimizing process bottlenecks, optimizing operating conditions, and implementing quality control measures. Process optimization can also involve utilizing the latest technologies and equipment, such as continuous flow reactors, in-line blending systems, and automated control systems.
Another way to maximize efficiency is to improve feedstock quality. This may involve implementing pre-treatment processes to remove impurities or contaminants from the feedstock, such as water, free fatty acids, and methanol. It may also involve sourcing high-quality feedstocks, such as waste oils or low carbon intensity feedstocks, that have consistent quality and low variability.
Reducing energy consumption is another way to maximize efficiency and profitability. This may involve implementing energy-efficient technologies, such as heat exchangers, heat recovery systems, and efficient lighting and HVAC systems. It may also involve utilizing renewable energy sources, such as solar or wind power, to reduce energy costs.
Finally, maximizing profitability requires optimizing the product quality and pricing strategy. This may involve conducting market research to identify customer needs and preferences, developing a strong brand and marketing strategy, and identifying opportunities to diversify product offerings or expand into new markets.
In summary, maximizing the efficiency and profitability of your biodiesel plant requires a comprehensive approach that involves process optimization, feedstock quality improvement, energy consumption reduction, and product quality and pricing optimization. By implementing these strategies, you can improve the plant's bottom line and contribute to a more sustainable future.
Comments